WORDS: PETER STEVENS | Photography: Peter Stevens, Patrick le QuÉment, envisage
That the form of some cars comes out looking exactly as the designer intended is not because of highly sophisticated computer-aided tools. It’s because a small team of design sculptors interpreted the original two-dimensional ideas and turned them into a three-dimensional object. This is the element of the design process that produces the wonderfully emotional forms which separate the mundane ‘white goods’ from the desirable rolling sculpture that some automobiles are.
Traditionally, sculptors would use clay to explore their three- dimensional thoughts. In order to do this, they’d make small models or ‘maquettes’ of their artistic ideas before starting to carve in marble. Carving in stone requires great skill because, not surprisingly, once cut from the block, material cannot be put back on to the sculpture. And, of course, the perfect piece of stone has always been expensive.
Many past sculptors would stare at their block of stone trying to imagine what was ‘inside’ it, before working with the maquette. However, the clay would quickly dry out and crack if it was not fired in a kiln, so in the late 19th century Plasticine was invented to modernise this process.
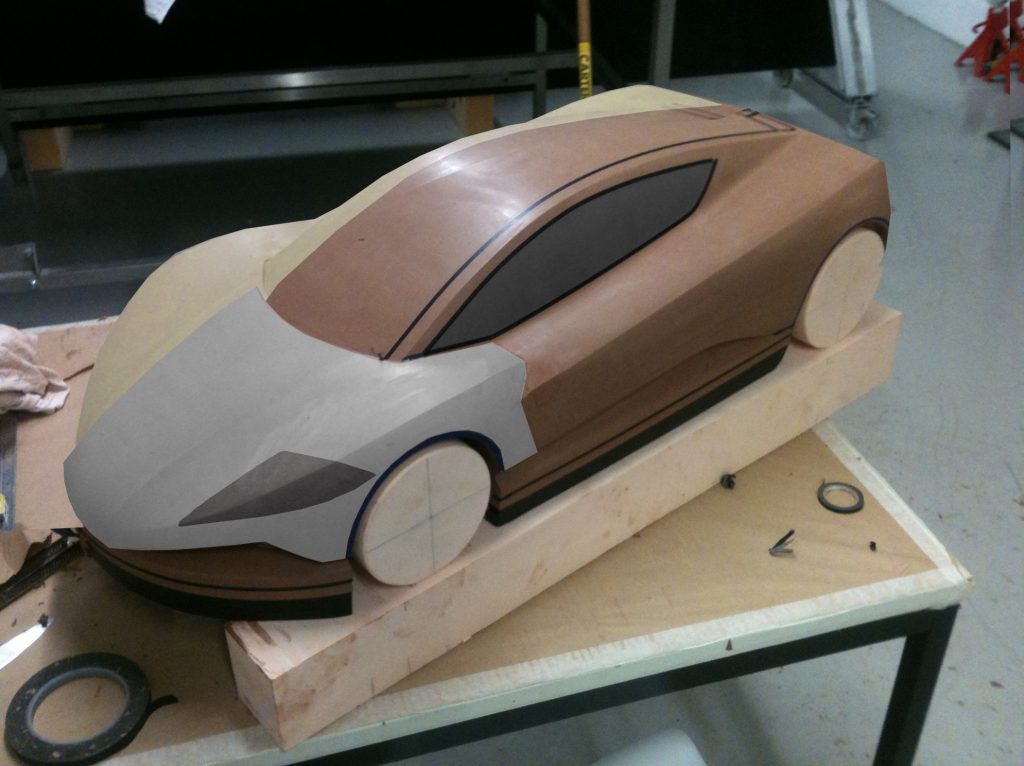
In the early 1890s, William Harbutt of Bathampton, UK, experimented with a mixture of oils, waxes and clay minerals to produce modelling Plasticine. Unlike the modelling clay used by ceramicists and sculptors, it couldn’t be fired in a kiln, because heat made it soften and disintegrate. Yet it could be easily worked with simple wire tools, and material could be added, removed or used again. Although Plasticine does slowly lose its malleability and cannot be very smoothly finished, it was much preferred to traditional clay.
Meanwhile, to further address the shortcomings of clay a different material, Plastilin, was developed and patented by German scientist Franz Kolb in 1880. And Plasteline was developed in France by Claude Chavant in 1892, and became a registered trademark in 1927. These materials became known as Industrial Plasticine, but today they are called modelling or styling clay and are widely used in automotive design studios for producing both scale and full-size models of future products.
The material contains wax, oils, clay flour, sulphur and lanolin. Because the clay has to be packed on to the base model at a temperature of approximately 80o Fahrenheit, inexperienced modellers risk getting major blisters on their hands. The lanolin softens the skin and the temperature then overheats it.
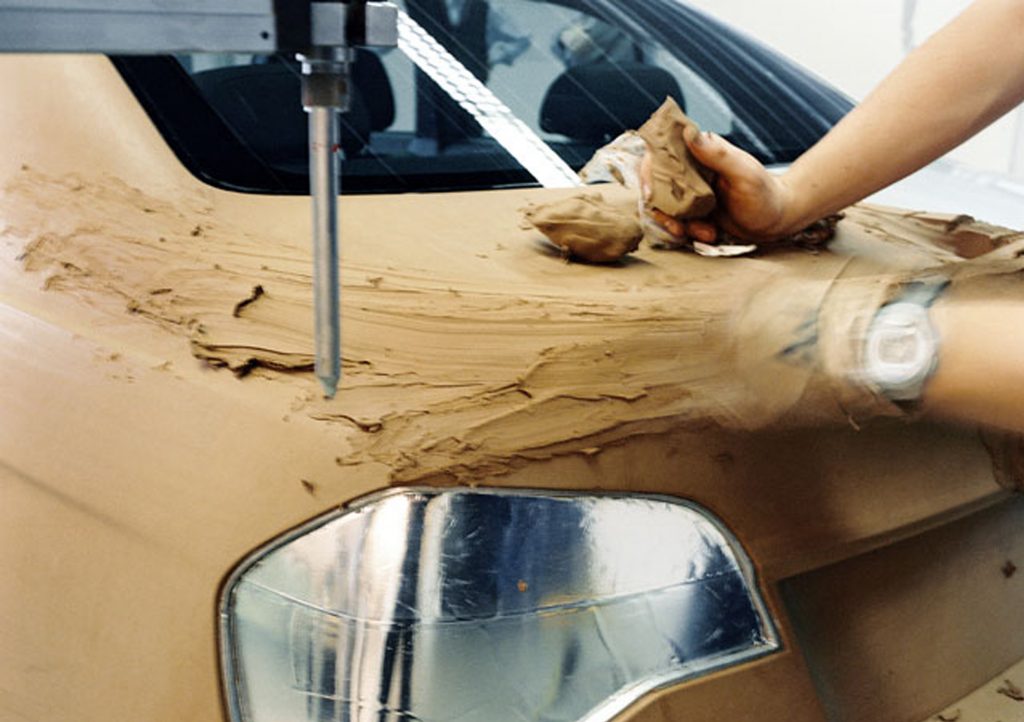
Until recently, the modelling process was done entirely by hand. A thick layer of pre-warmed styling clay was laid on to a buck or armature created from wood and polyurethane foam or high-density polystyrene. The clay was then carved by highly skilled sculptors using ever- more refined tools, until a perfectly surfaced form was produced.
In recent times, computer-aided machining is used to create a basic design form from data derived from an initial Alias 3D CAD model, generated by either the designer or, more commonly, a studio Alias specialist. After the hardened clay has been roughly machined, the sculptors then take over the model development guided by the designer.
The relationship between the designer and model maker is a crucial element. The designer has to demonstrate that he knows exactly what he wants the form to be, and the clay sculptor needs the skill to interpret that concept into three dimensions. Quite often that successful understanding of the designer’s intentions by the clay sculptor, and the development of a close working relationship, can ‘make’ the young designer’s name – just as a poor working relationship can limit their career prospects.
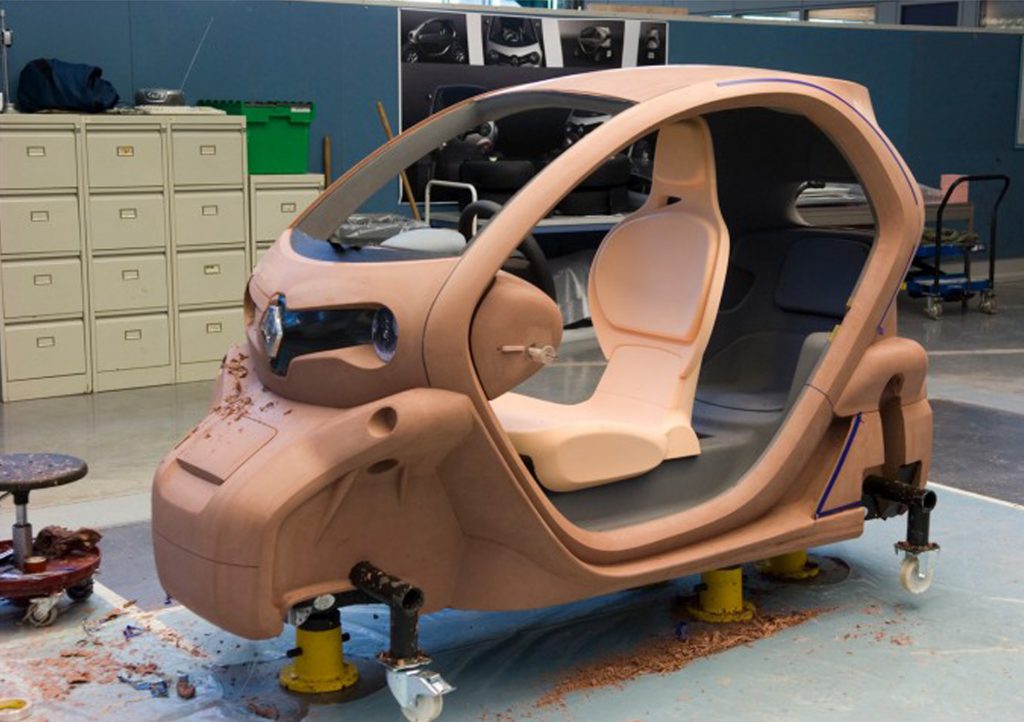
Three-dimensional design using only the computer and a CAD modelling programme can easily produce extremely badly resolved forms and surfaces. However, a skilled modeller will have the experience to guide the designer and point out surface treatments that cannot be made to ‘work’ in three dimensions. The computer has no such experience.
Harley Earl, founder of the Art and Color Section at General Motors, is credited with introducing clay modelling to the automotive design studio. In the late 1920s and 1930s GM executives viewed Earl’s conceptual ideas as flamboyant and without any sense of reality. Earl struggled to legitimise his design methods against the conservatism of production-oriented executives.
As head of the newly formed section, he was initially referred to as one of the “pretty-picture boys”, and his design studio as being the “beauty parlour”. But with the support of GM president Alfred P Sloan he persevered, and these days all designers owe a debt of gratitude to this colourful man, for establishing the credibility of the design process.
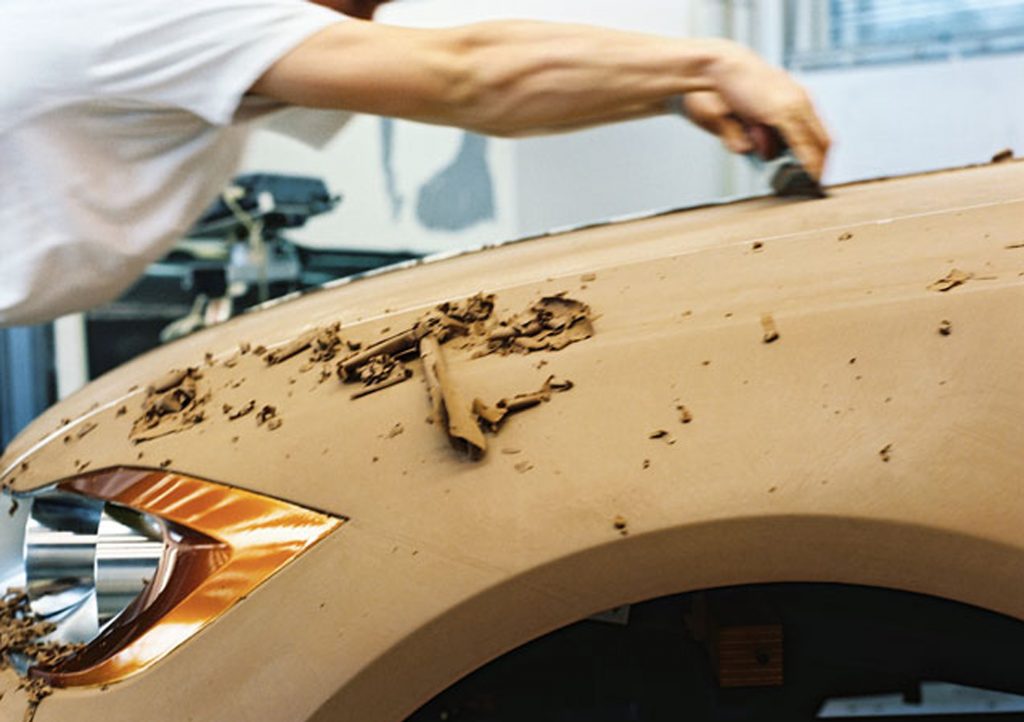
One of the problems with working with styling clay is that it isn’t an easy material to ‘read’ unless you are used to the flat appearance of a clay model. For people in the automotive design industry, clay is simply a means of communicating or evaluating a form. It’s a language they understand. But for those for whom the medium is new or ‘foreign’, the form can be just a dull, undecipherable shape.
Some help is at hand for those people; a thin, flexible, plastic sheet called Dynoc. This magical material is almost like a sheet of paint, which after being soaked in water can be carefully stretched over the model to give the impression of a painted vehicle. Dynoc enables the designer to observe, develop and gain control of reflections on the model’s surface – a lengthy but ultimately extremely satisfying process.
Many automotive companies start a project by developing a number of scale models. Frequently used scales include 1:5, 1:4 or sometimes 1:2.5, and half-models are often produced in order to save time. Only one side of the car is modelled, and when this is placed up against a vertical mirror the complete form can be appraised. However, this isn’t a particularly successful method, because the centreline can always be viewed.
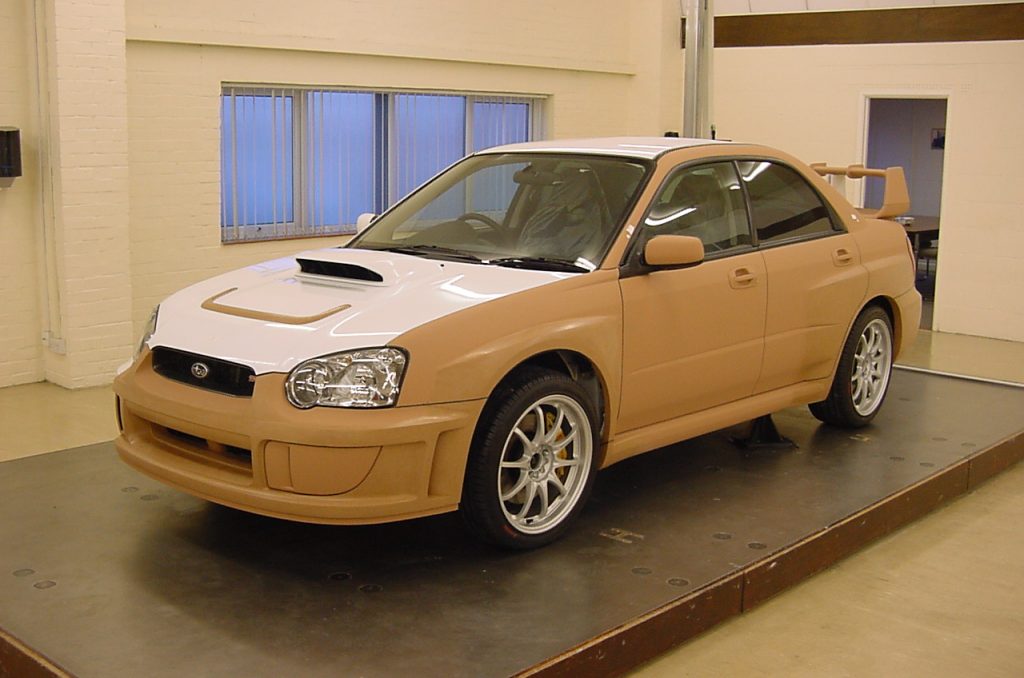
It is from these models that dimensional data can be taken and then used to machine the full-size clay design model – and it’s only at this point that the true design form can be developed. In order to show the outlines of the windscreen and side and rear glass, as well as the most important graphic details of the design, black crepe tape (similar to black masking tape) is used.
This can be stuck to the clay and is easily moved as part of the design process. The tape is also used to develop the principal style lines; the defining edges between surfaces. Applying perfect tape-lines is a most satisfying aspect of the early stages in developing a design theme.
The career opportunities offered by becoming a clay sculptor are often overlooked or misunderstood by secondary-school teachers. With the chance to be so closely involved in the design process, a good modeller can play a large part in developing a successful automobile design, which can be very rewarding.
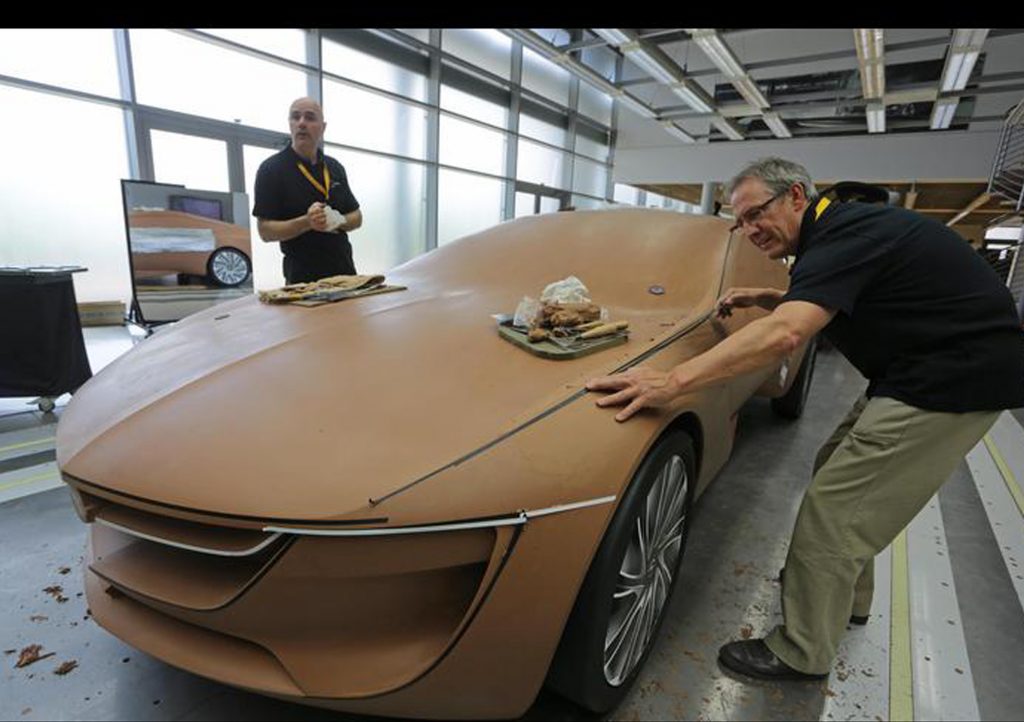
It’s a troubling fact that many design colleges now no longer consider clay work to be an essential part of a student’s development, believing that everything can be done using CAD. Meanwhile, some design studios briefly considered going straight from digital models to tooling without ever seeing what the completed car would look like – but thankfully designers have strongly opposed this idea.
There is a shortage of young design sculptors at present, so there needs to be a proper, affordable training course for young people who love the idea of being part of the creative process but perhaps can’t afford the very high student fees being asked by design colleges. Such a course would require a design element as part of the curriculum, to give the students the opportunity to understand the complete process.
If this doesn’t happen, those in the auto industry who are concerned only with shortening the ‘time to market’ may have their way, and the art may disappear from car design. It’s vital to remember that the computer, while being a useful tool, is just a box filled with wires, plastic and sand; there are no ideas inside that enclosure. They are in the designer’s head and in the sculptor’s hands.