WORDS: DAVID LILLYWHITE | PHOTOS: SIMON THOMPSON
“I love clay,” says Alfa Romeo’s senior exterior designer Alexandros Liokis. “Cars will always be emotional objects, so there’s nothing like having a physical model. Clay is still an important part of the process.”
This article first appeared in Magneto 20.
Alexandros, Greek-born and now living in Italy with a mind-boggling array of classic cars in his garage, is demonstrating the processes he goes through to design a car. You won’t be surprised to hear that most of his tools are high-tech, including a digital sketch pad that he uses to work up initial ideas, and a virtual-reality system employed to envisage interior designs in particular.
And yet, Alexandros comes to life at the full-size clay Tonale in the centre of one of Alfa’s usually secret Centro Stile studios. He and clay modeller Lorenzo Sibille demonstrate how the shape can be changed with the most rudimentary of tools – a Surform file and a collection of metal spatulas – as they patiently sculpt the soft clay under the studio lights.
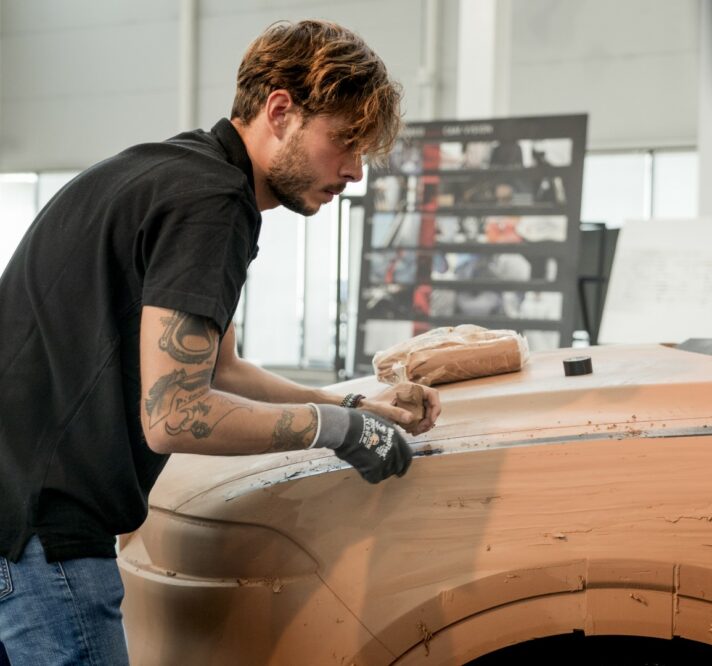
The shape can be changed with the most rudimentary of tools – a Surform file and a collection of metal spatulas
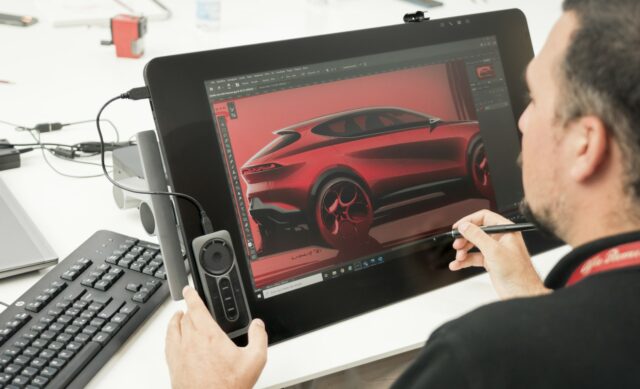
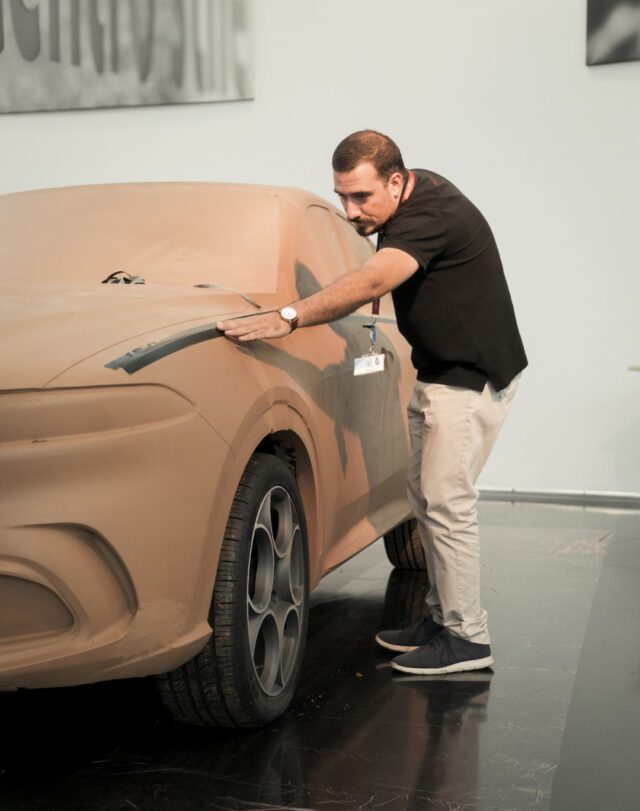
Then the shaping tools are handed over. To anyone whose formative automotive experiences involved filling dents or replacing rusty metal, the process doesn’t feel so different to working body filler (or bondo). But the difference is that the clay is firmer and smoother, easier to shape but harder work physically. A firm, steady hand is needed – and it’s best not to wear your best shoes, because the shavings of clay fall all around. It’s a wonderfully satisfying process.
These full-size clay models start out as a metal frame with the engineering ‘hard points’ – those dimensions that are non-negotiable – built in. On top of this structure goes a polyurethane foam, and over that a 25mm-thick layer of clay. It leaves little room for error; the sculptor who breaks through the clay into the foam will not be popular. And this also means the idea of a body shape being wholly created on a full-size clay is largely false.
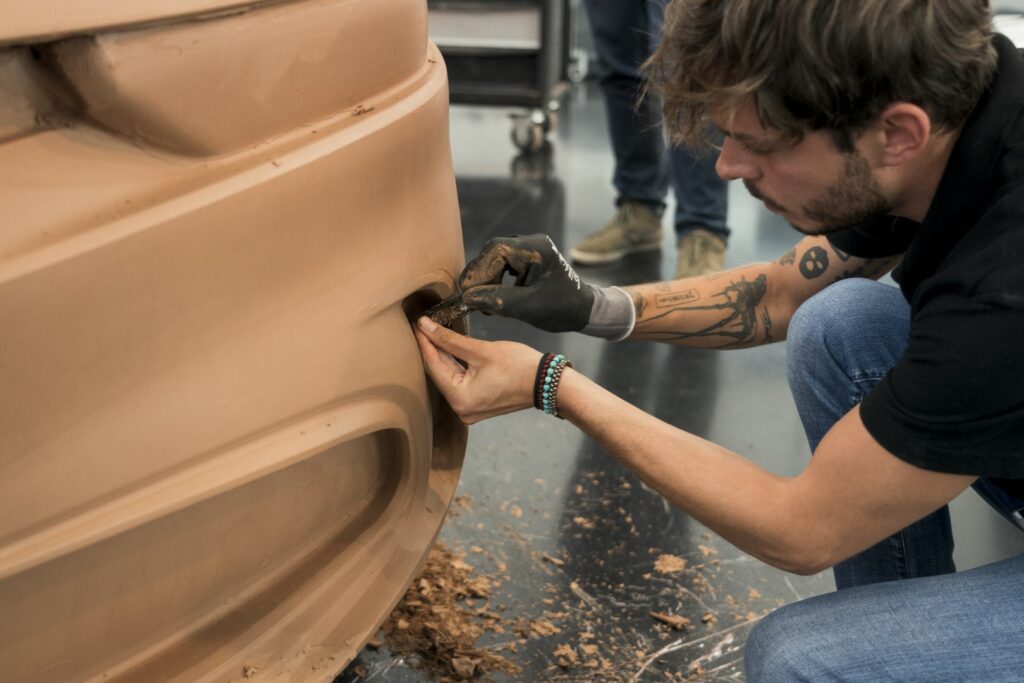
Instead, the shape begins with sketches, which are then digitally rendered into 3D, going through countless processes to create a shape that works from visual, engineering, aerodynamic and safety perspectives. Only after this hugely involved and lengthy work will the clay be wheeled out. Often it’ll be subtly different from one side to the other, to enable different designs to be tried – and it’s now that the subtleties of creases and curves are gently tweaked.
Alexandros says: “To know that a crease is good, you have to touch it,” but it also needs to reflect the light satisfactorily. For that, sheets of thin Di-Noc film are dipped in a water bath and then carefully smoothed into place. A shiny grey is favourite to gauge reflections, with black used for the windows and graphics. The clay will be wheeled outside into the daylight and examined all over, often to be changed again and again over a period of two or three months.
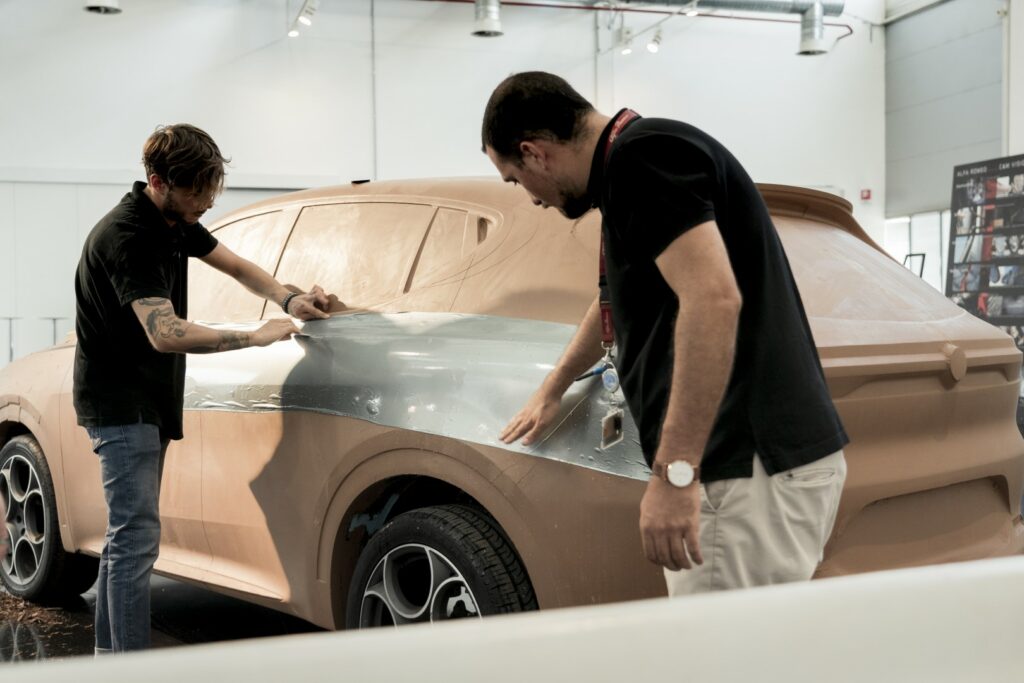
And what happens to the clay after all this? It’s stored away, to re-emerge when a facelift is due – perhaps a new bumper or lights. When no more iterations are needed, the clay will be recycled for the next new car and the process will start all over again.